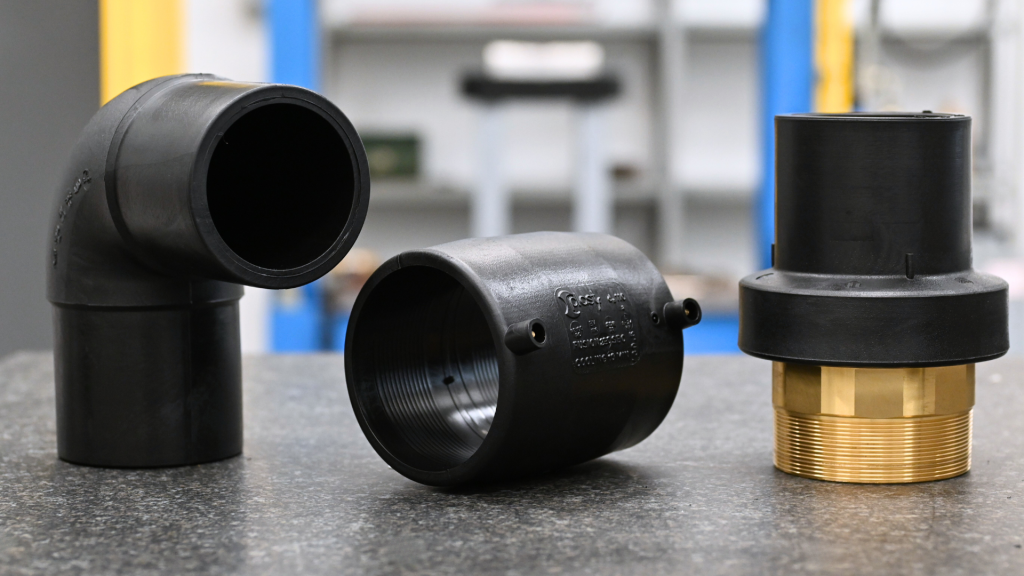
Polyethylene (PE) pipe fittings are essential components in modern fluid transport systems. Whether for water, gas, or industrial use, selecting the right type of fitting helps ensure durability, safety, and performance. This article explores what PE pipe fittings are, how they differ from other materials, and how to determine the most effective solution for your infrastructure project.
PE fittings have become a preferred choice in civil and industrial sectors due to their excellent adaptability and ease of installation. Their ability to withstand pressure and corrosion makes them ideal for both new constructions and retrofit projects.
What are PE Pipe Fittings?
PE pipe fittings are used to join sections of polyethylene piping in a safe, sealed, and durable manner. They enable directional changes, transitions between diameters, and secure terminations within the system.
These fittings are fundamental to building systems that are both flexible and long-lasting. Their use spans from small residential water lines to large-scale industrial distribution systems. They can be molded into a wide range of geometries to accommodate complex layouts and system constraints. Whether used above or below ground, PE fittings offer excellent adaptability to movement, vibrations, and environmental exposure.
They are also available in different pressure ratings and material density, making them suitable for diverse environmental demands. They contribute to the overall efficiency and safety of the system by minimizing leak risks and supporting fast, secure installations.
Differences between LDPE and HDPE Pipe Fittings
While both LDPE and HDPE fittings are made from polyethylene, HDPE (High-Density Polyethylene) offers higher rigidity, strength, and pressure resistance. Standard LDPE fittings are often used in low to medium pressure systems, whereas HDPE fittings are favored in high-pressure and critical environments.
LDPE fittings typically have a lower density and are slightly more flexible, which makes them suitable for systems that do not require intense mechanical resistance. HDPE, with its high-density structure, performs better in more aggressive settings where mechanical strength and tight seals under pressure are mandatory. Understanding these differences allows engineers and contractors to optimize material selection based on system requirements.
Why HDPE Fittings are preferred for water and gas systems
HDPE pipe fittings are widely used in water supply and gas distribution systems due to their flexibility, corrosion resistance, and long service life. Unlike metal alternatives, PE fittings do not rust or degrade from moisture or gas exposure.
The material’s resistance to external stress and its chemical stability ensure a longer operational cycle without the need for frequent replacement. In gas systems, where safety is paramount, HDPE fittings deliver consistent performance even under variable temperature and pressure conditions. For water networks, the smooth internal surface of HDPE reduces pressure drops, contributing to overall system efficiency.
Types of HDPE Pipe fittings and their uses
Choosing the correct fitting type for your application ensures system integrity and operational efficiency. Below are some of the most common fitting types used in HDPE piping systems.
The choice of fitting depends not only on the type of connection required but also on the nature of the fluid, installation method, and surrounding conditions. From simple elbows and tees to complex transition fittings, each component plays a key role in maintaining performance across the system. These fittings are available in various diameters, pressure ratings, and connection styles to fit specific technical needs.
Electrofusion vs. Spigot vs. Transition Fittings
Electrofusion fittings are widely adopted for their ability to create strong, welded connections using embedded heating wires. They are suitable for both underground and pressurized systems.
Spigot fittings are designed for butt welding and offer excellent strength for permanent installations. They are often chosen when mechanical loads or system pressure demand a high degree of structural integrity.
Transition fittings are used to connect HDPE pipes to different materials, such as steel, allowing hybrid systems without compromising sealing or performance. These are especially useful in retrofit projects where complete system replacement isn’t feasible.
Electrofusion Fittings and their benefits
Electrofusion fittings offer consistent performance in demanding environments. Their ease of welding, resistance to external agents, and high-pressure tolerance make them suitable for a wide range of installations, including water systems, gas systems, and industrial lines.
They are also compact, reducing the space required during installation. Electrofusion joints are known for their reliability and repeatability, making them ideal for automated or large-scale operations. Additionally, these fittings help reduce human error during assembly due to their design and precise welding process.
Choosing the right HDPE Pipe Fitting for your application
Project requirements vary, so choosing the correct fitting involves evaluating technical specifications and installation constraints.
In addition to pipe diameter and pressure ratings, engineers must account for external factors such as exposure to sunlight, underground soil composition, and temperature fluctuations. Installation conditions (e.g., confined spaces or remote areas) may also affect the fitting selection, particularly in determining whether electrofusion or butt funsion welding is more feasible.
Factors to consider: size, pressure, and material
When selecting a fitting, ensure compatibility with the pipe’s diameter, SDR (Standard Dimension Ratio), and PN (Nominal Pressure). For example, PE100 fittings are commonly used for their higher pressure tolerance and superior performance.
Sizing errors or mismatched components can compromise the system’s integrity and result in costly repairs. It’s also essential to source fittings from certified manufacturers who follow international standards, ensuring long-term reliability and traceability. Material choices can also influence resistance to UV exposure, temperature variations, and contact with specific gases.
When to use electrofusion, spigot, or custom fittings
Electrofusion fittings are ideal for underground pipelines, gas distribution systems, and critical environments. Their reliability and ease of use make them the go-to solution for situations where precision and safety are essential.
Spigot fittings work well in long-run installations where pipe sections can be aligned and welded in sequence. They are also preferred in applications requiring strong, monolithic welds.
Customised fittings come into play when a standard product cannot address the design constraints of the project, allowing tailored geometries and material specifications for optimal results.
Installation and maintenance of HDPE Pipe Fittings
Proper installation is crucial for maximizing the lifespan and effectiveness of HDPE fittings.
Correct procedures not only ensure structural integrity but also reduce the risk of future system failure. Skilled labor, the right equipment, and compliance with safety protocols are non-negotiable for the successful implementation of HDPE piping systems. Moreover, periodic maintenance and visual inspections help detect early signs of wear or misalignment.
Proper welding and welding techniques
Welding must be carried out by trained personnel using certified machines. Electrofusion welding involves aligning the pipe and fitting, applying heat through embedded coils, and maintaining pressure for a defined period. Each weld must be tested for integrity before commissioning.
Best practices include pipe surface cleaning and the use of calibrated equipment. In many cases, welders follow a checklist to ensure consistent results across all connections. Records of weld data are also often maintained for quality assurance and traceability.
Common mistakes to avoid
Some of the most frequent errors include improper pipe surface preparation, misalignment during welding, and incorrect pressure application. These can compromise the sealing and longevity of the connection.
Other mistakes include neglecting ambient temperature effects during welding and skipping post-weld cooling times. Using non-calibrated machines or working with contaminated pipe surfaces can also compromise welding. Educating welders and performing regular audits can significantly improve the reliability of the entire system.
Conclusion: making the right choice with Plastitalia
HDPE pipe fittings are a foundational element in fluid distribution systems. Selecting the right type, size, and installation method helps ensure efficiency, safety, and longevity.
At Plastitalia, we specialize in manufacturing a wide range of high-quality polyethylene fittings, designed and tested for diverse applications in water, gas, and industrial piping systems. Our expert team offers in-depth technical support and customised solutions to meet the specific requirements of each project.