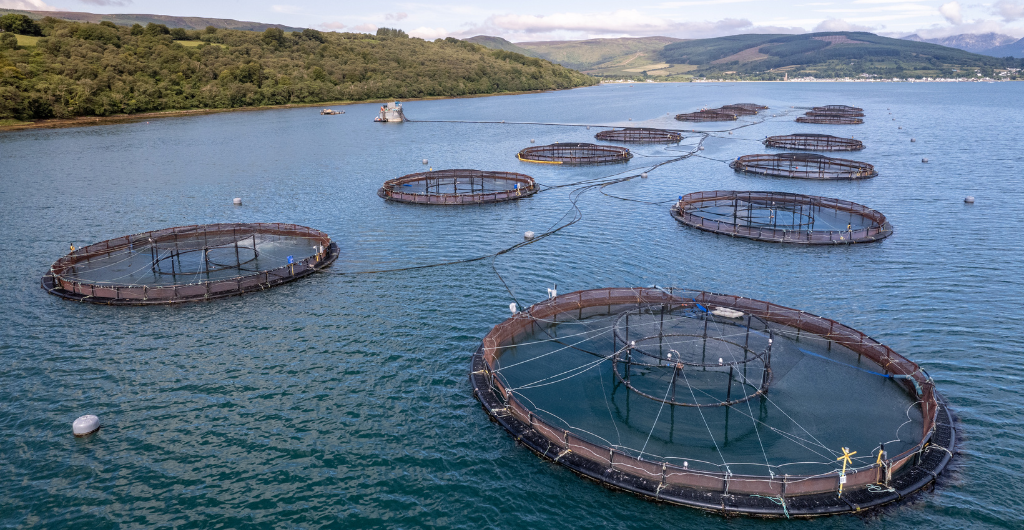
In the rapidly growing world of aquaculture and marine infrastructure, choosing the right materials for piping systems is essential for the success of operations. HDPE piping solutions offer unparalleled performance for aquaculture farms and marine environments. Known for their durability, flexibility, and resistance to harsh conditions, HDPE pipes and fittings are ideal for water transport and distribution systems used in fish farming, industrial applications, and critical marine infrastructure.
This article explores why HDPE is the best material for marine and aquaculture applications, its key benefits, and how it outperforms other materials, ensuring long-lasting and reliable performance.
Why HDPE Is the best choice for Aquaculture and Marine environments
HDPE (High-Density Polyethylene) has become the standard material for piping systems in aquaculture and marine environments due to its exceptional properties. The material is specifically designed to handle the unique challenges that come with these sectors, such as exposure to seawater, chemicals, and extreme conditions.
Its resistance to biofouling and low maintenance requirements make it especially suitable for submerged or hard-to-access installations. Unlike traditional materials, HDPE does not degrade over time when exposed to marine organisms or constant humidity. These qualities contribute to more stable operations and significantly reduced downtime in aquaculture facilities.
Corrosion resistance against seawater and chemicals
One of the primary advantages of HDPE is its corrosion resistance. Unlike metals, HDPE does not rust or corrode when exposed to seawater or various chemicals found in industrial settings. This is crucial in aquaculture and marine applications, where pipes are constantly exposed to saline environments and aggressive chemicals.
HDPE pipes offer a long-term, low-maintenance solution for transporting water in fish farms, cooling systems for marine facilities, and undersea pipelines. With HDPE, there is no risk of degradation over time due to exposure to salts or other corrosive substances.
Flexibility and strength in harsh conditions
HDPE is incredibly flexible, making it ideal for systems that need to accommodate ground shifts, seismic activity, or water flow pressure. This flexibility ensures that HDPE piping remains intact and functional, even under demanding conditions such as fluctuations in temperature, soil movement, or underwater currents.
Furthermore, HDPE pipes can withstand high-pressure applications while maintaining their shape and strength, ensuring the integrity of piping systems in marine environments where stresses are common.
Key applications of HDPE Pipes in Aquafarming
HDPE pipes have become a staple in the aquaculture industry due to their versatility and performance. From fish farming to marine cooling systems, HDPE offers a reliable and durable piping solution for various applications.
Their ability to withstand UV exposure, high salinity, and biological agents makes them ideal for both offshore and land-based aquaculture systems. HDPE pipes also support modular installations, allowing facilities to scale and reconfigure layouts with minimal disruption. This flexibility is especially valuable in dynamic environments like fish farms and integrated marine operations.
Fish farming water supply and distribution systems
In fish farming, the water supply and distribution system is the backbone of the operation. HDPE piping systems are used to transport water to fish tanks and regulate water flow efficiently. The flexibility and resistance to corrosion of HDPE ensure that water quality remains optimal, reducing the risks of contamination and maintaining fish health.
HDPE also ensures continuous water circulation, preventing stagnation and ensuring that fish are provided with clean and oxygenated water, which is vital for their growth and survival.
Tank Plumbing and underwater installations
Another key use of HDPE pipes in aquaculture is for tank plumbing and underwater installations. These applications require a material that can withstand constant exposure to water, pressure, and corrosive substances. HDPE pipes are ideal for these uses due to their long-term performance and ability to endure extreme underwater conditions.
In addition, HDPE’s flexibility allows it to be easily installed in complex, tight spaces or underwater setups, ensuring that plumbing systems function efficiently and without leaks.
Advantages of usiung marine-grade HDPE Fittings
Marine-grade HDPE fittings are essential for ensuring reliable, leak-free connections in aquaculture systems and marine infrastructure. These fittings are specifically designed to withstand the harshest marine environments, offering high-performance solutions for water distribution and other critical applications.
They are engineered to maintain mechanical strength and sealing integrity even under prolonged exposure to saltwater and extreme temperatures. Their non-toxic composition also makes them safe for use in systems involving live aquatic organisms. Combined with electrofusion technology, these fittings provide consistent results in both static and dynamic marine systems.
Long-Term durability and minimal maintenance
Marine-grade HDPE fittings offer superior durability, ensuring that pipes and fittings last for decades with minimal maintenance. The long lifespan of these fittings reduces the need for frequent repairs or replacements, which is especially important in remote aquaculture or marine facilities where maintenance can be costly and time-consuming.
Additionally, HDPE fittings are resistant to environmental stress cracking, making them suitable for use in high-pressure systems that experience fluctuating conditions and potential mechanical stress.
Ease of Installation and welding techniques
One of the reasons marine-grade HDPE fittings are so popular is their ease of installation. HDPE pipes and fittings can be welded with ease using advanced electrofusion techniques, which ensure strong and secure joints. This minimizes the risk of leaks and maximizes the longevity of the piping system.
The process of electrofusion welding involves heating the fitting and pipe, ensuring uniform strength across the system. The simplicity and efficiency of this method make HDPE a cost-effective and time-saving solution for large-scale aquaculture and marine infrastructure projects.
Designing Efficient Aquaculture Piping Networks
When designing aquaculture piping networks, choosing the right materials and installation techniques is critical to ensure optimal performance. HDPE offers the flexibility, durability, and resistance needed to handle the demanding conditions of aquaculture systems, ensuring a reliable and safe water transport system.
A well-designed HDPE network supports efficient water flow, minimizes energy consumption, and simplifies future maintenance or expansions. Its adaptability to varied terrain and integration with automation systems further enhances operational control. This makes HDPE the preferred solution for both small-scale hatcheries and large industrial fish farming complexes.
Selecting the right HDPE grades and standards
When selecting HDPE pipes for aquaculture and marine applications, it’s essential to choose the correct material grade. PE100 is the most commonly used material for high-pressure and critical environments due to its superior strength and resistance to chemicals.
Moreover, HDPE standards such as PN ratings (Pressure Nominal) must be considered when designing piping systems, as they determine the pipe’s pressure-bearing capacity. Ensuring that the correct grade and pressure rating are selected is crucial for the safety and longevity of the system.
Ensuring Longevity in Marine Environments
To ensure the longevity of the HDPE piping system, it is vital to take into account the specific environmental conditions it will face. In marine environments, exposure to saline water, UV radiation, and marine life can accelerate the degradation of some materials. HDPE, however, is UV resistant and able to withstand the corrosive effects of seawater, making it the material of choice for underwater and exposed installations.
Additionally, the flexibility of HDPE allows it to adapt to shifting environments, reducing the risk of cracks or leaks that can arise from ground movement or other environmental factors.
Conclusion
HDPE piping systems are an indispensable part of modern aquaculture and marine infrastructure due to their outstanding performance in harsh conditions. Whether used for fish farming water supply, underwater plumbing, or industrial marine applications, HDPE offers long-term reliability, low maintenance, and cost-effectiveness.
As the demand for sustainable and efficient infrastructure grows, HDPE’s unmatched advantages ensure that it will remain the preferred material for aquaculture and marine applications in the years to come.
For businesses seeking scalable, future-proof solutions, HDPE represents a smart investment backed by proven field performance. Its compliance with international standards and adaptability to custom engineering needs make it suitable for even the most complex aquatic systems. As the aquaculture industry evolves, HDPE will continue to support innovation, safety, and operational excellence.