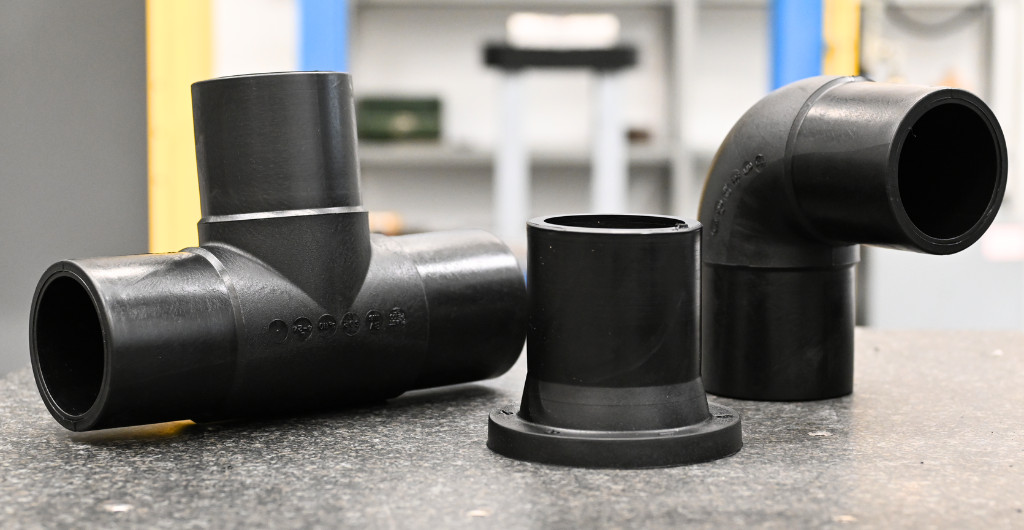
HDPE fittings play a crucial role in building safe and efficient piping networks. In this guide, you’ll discover what they are, how they compare to other materials, where they’re used, and how to choose the right type of fitting for your project.
What Are HDPE Fittings and How Do They Work?
Let’s start with the basics. Understanding what HDPE fittings are and how they function is key to selecting the right components for your pipeline system.
These fittings are designed to connect high-density polyethylene pipes safely and efficiently. They are available in a variety of configurations and sizes to suit diverse system requirements. The installation method, whether through welding or mechanical connection, plays a crucial role in the performance of the entire systems.
Understanding the Role of HDPE Fittings in Piping Systems
HDPE fittings are essential components for creating strong, leak-proof joints in high-density polyethylene piping systems. They ensure consistent flow, structural stability, and long-term durability in transporting water, gas, and other fluids. These fittings come in various forms, including bends, tees, reducers, and couplings, each designed to serve a specific function. Their flexibility and resistance make them ideal for both buried and exposed systems.
They are particularly effective in dynamic environments, where ground movement or vibration might compromise traditional connections.
In pressurized systems, the integrity of each joint is vital to avoid leaks, which HDPE fittings help to prevent.
As infrastructure modernizes, HDPE’s adaptability makes it suitable for integration into both legacy and newly engineered networks.
Key Benefits of HDPE Fittings: Durability, Flexibility, and Corrosion Resistance
Unlike metal alternatives, HDPE fittings resist corrosion and chemical attack, even in aggressive environments. They offer flexibility, excellent impact resistance, and an impressive lifespan—often exceeding 50 years. Their smooth inner surfaces minimize friction losses and promote energy-efficient transport of fluids. Moreover, HDPE is not subject to the action of chemicals, contributing to lower maintenance over time.
This makes HDPE an excellent choice for systems requiring long operational cycles with minimal intervention.
Its elasticity allows it to absorb shocks or stress from ground shifting or water hammer effects.
These advantages translate into lower operating costs, fewer repairs, and greater peace of mind for operators and engineers.
HDPE vs Other Materials: Why Choose HDPE Fittings?
With so many materials available for piping systems, why is HDPE increasingly preferred? Here, we compare HDPE with other common materials to understand its unique advantages.
Choosing the right piping material can impact the system’s durability, efficiency, and maintenance costs.
HDPE has become a trusted solution in various industries thanks to its superior resistance, lightweight structure, and long service life. It adapts well to harsh environments where other materials tend to degrade or require additional protection.
Comparison with PVC, Metal, and PP Pipe Fittings
Compared to PVC, HDPE is more resistant to pressure and temperature variations. While PVC becomes brittle in cold climates, HDPE retains its flexibility. Unlike metal fittings, HDPE does not corrode or require protective coatings. Galvanized steel or cast iron fittings, while durable, are heavier, harder to install, and prone to internal corrosion. Compared to polypropylene (PP), HDPE is generally stronger, more UV-resistant, and better suited for buried pipelines and pressurized systems.
Its lower weight simplifies logistics and allows faster on-site handling, especially in remote or hard-to-reach locations.
In terms of safety, HDPE’s integrity under pressure minimizes the risk of rupture or sudden failure.
For projects requiring long-term reliability with minimal environmental impact, HDPE outperforms many traditional alternatives.
Environmental and Cost Benefits of HDPE
HDPE fittings are lightweight, reducing transportation and installation costs. They require less energy to produce and generate fewer emissions throughout their lifecycle. Their long life expectancy further reduces total cost of ownership. Municipalities and private companies that adopt HDPE fittings often benefit from reduced system downtime and fewer repairs.
This makes HDPE an excellent choice for projects with sustainability goals or green building certifications.
Because HDPE systems are modular and easy to expand, they support scalable infrastructure with low added costs.
Additionally, the reduced frequency of replacement and repair limits the environmental disruption during maintenance.
Best Applications for HDPE Fittings
HDPE fittings can be used in a wide range of sectors and environments. This section explores the main industries where these fittings deliver exceptional performance.
Their versatility makes them suitable for both public and private infrastructure projects. From clean water delivery to gas transport, HDPE fittings ensure operational reliability across multiple contexts. Thanks to their modularity and ease of installation, they are ideal for both new systems and retrofitting existing pipelines.
Water Supply and Wastewater Systems
HDPE fittings are widely used in municipal water distribution systems thanks to their resistance to microorganism growth and ease of maintenance. They are also suitable for wastewater collection and drainage, including stormwater systems. Their ability to withstand ground movement without cracking makes them ideal for urban and rural infrastructure.
Gas Distribution and Industrial Pipelines
In gas systems, safety is critical. HDPE fittings, especially when welded by electrofusion, provide secure, leak-free joints. Their flexibility reduces the risk of pipe breakage due to soil settlement or seismic activity. In industrial plants, these fittings handle aggressive chemicals and maintain performance even under mechanical stress or temperature fluctuations. Industries such as mining and energy increasingly adopt HDPE solutions.
Agricultural and Irrigation Networks
Farmers and agritech companies value HDPE fittings for their ease of installation and resistance to UV rays and fertilizers. They are widely applied in irrigation systems, aquafarming, and greenhouses. In large-scale irrigation projects, HDPE’s lightweight nature and quick jointing methods significantly reduce labor costs. In remote areas, the material’s resilience to rough terrain and shifting soil conditions makes it the material of choice.
Emerging Applications in Data Centers and Renewable Energy
With the growth of digital infrastructure, HDPE fittings are now being used in cooling systems for data centers, where thermal stability and reliability are key. In renewable energy sectors, such as biogas and hydroelectric systems, HDPE’s chemical resistance and leak-proof jointing support safe and clean operations.
How to Select the Right HDPE Fittings for Your Project
Not all HDPE fittings are the same. This section helps you understand how to evaluate your project’s needs and make the best choice for performance and durability.
Proper selection is essential to ensure system integrity, safety, and long-term efficiency.
The choice depends on multiple factors, including pipe dimensions, operating conditions, and connection techniques.
Understanding these variables helps reduce maintenance costs and prevents premature system failure.
Pressure Ratings and Pipe Compatibility
Each HDPE fitting must match the pipe’s diameter, thickness (SDR), and pressure rating. The most common standards include PE100 materials and PN ratings, which indicate pressure limits. Misaligned selections can lead to leaks or reduced performance over time. It’s essential to consult pressure-temperature correlation charts and installation manuals to ensure proper compatibility.
Selecting the wrong rating can compromise the entire system, especially under variable load or pressure surges.
For critical infrastructure projects, pressure testing during commissioning is also recommended.
Working with certified suppliers ensures access to fittings that meet national and international standards.
Choosing Between Electrofusion, Spigot, and Compression Fittings
- Electrofusion fittings use embedded heating elements for seamless, durable joints. They are ideal for underground installations and high-pressure lines.
- Spigot fittings require butt fusion welding and are perfect for long-distance pipelines.
- Compression fittings are often used for temporary or small-diameter applications.
Each type has its ideal context, and expert guidance ensures optimal performance. Additionally, environmental factors such as temperature extremes, humidity, and soil composition should be considered in the selection process.
The method of connection influences the system’s long-term reliability and maintenance needs.
In remote areas or urgent repairs, electrofusion fittings offer a fast and flexible alternative.
For permanent infrastructure, fusion welding remains the gold standard in terms of structural integrity.
Conclusion: HDPE Fittings as a Strategic Choice
HDPE fittings represent a strategic investment for companies and public entities managing water, gas, or industrial systems. Their durability, safety, and ease of installation make them an excellent solution for both new projects and system upgrades.
Choosing the right fittings depends on multiple factors—system pressure, diameter, environmental conditions, and welding technique. With decades of experience and technical know-how, Plastitalia supports clients in selecting, designing, and implementing polyethylene piping systems tailored to their needs.
Whether you’re building a municipal water line, an industrial cooling circuit, or a sustainable agricultural system, HDPE fittings offer unmatched reliability and long-term savings.