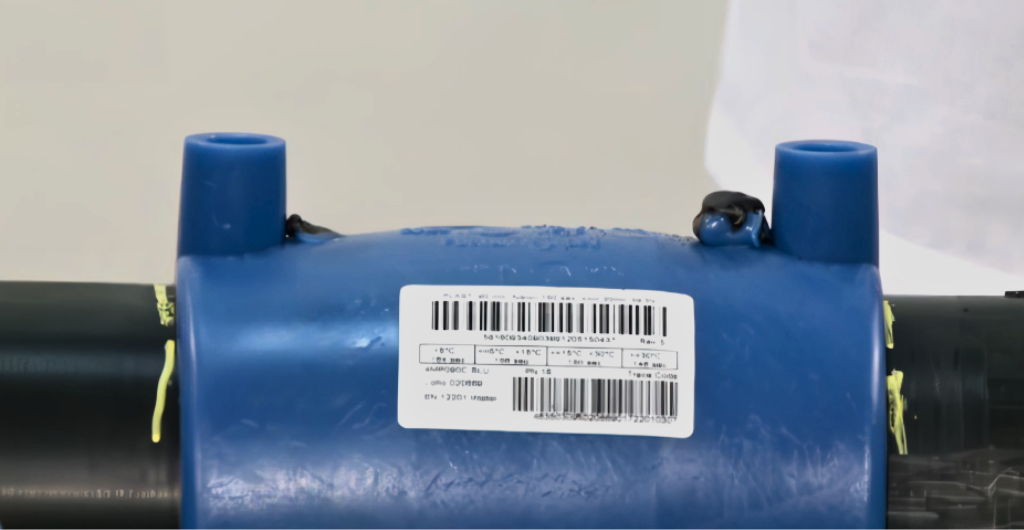
Electrofusion welding is a fundamental process for joining polyethylene piping and fittings. This process requires careful execution to avoid errors that can compromise weld quality and durability. In this article, we will take a detailed look at the main errors that can occur during the electrofusion welding process and their consequences.
Electrofusion welding errors are caused by four main factors:
- Incorrect preparation of the items to be welded: lack of cleaning, scraping or aligning the pipes and fittings can compromise the weld.
- Incorrect execution of the welding procedure: the use of inappropriate techniques that can compromise the proper fusion of materials.
- Wrong application of welding parameters: parameters such as time, temperature and pressure must be set correctly to ensure the best result.
- Possible problems related to the welding machine: technical problems due to lack of maintenance of the welding machine, but also accidental events such as a power failure, can affect the final result.
1. Short circuit during welding
Short circuit is one of the most serious consequences that can occur during welding. It is often due to errors during the preparation of the elements to be welded or incorrect setting of the fusion parameters.
- Incorrect insertion of pipes or spigot fittings.
- Lack of respect for the hot and cold areas of the fitting.
- Forcing the elements to be welded into the fitting.
- Use of a pipe whose end tightens.
- Misaligned pipes or spigot fittings.
- Use of too ovalized pipes.
- Incorrect transfer of fusion parameters to the welding machine.
2. Fitting detachment after the fusion cycle
Fitting detachment occurs when there isn’t an adequate fusion between the pipe and the fitting, usually due to poor preparation of the elements or contamination of the surfaces to be welded.
- Incorrect or failed scraping operation.
- Contaminated scraped area.
- Incorrect transfer of fusion parameters to the welding machine.
3. Pressure loss in the system
A plant pressure loss is often caused by errors made during pipe preparation, especially in the scraping stage.
- Wrong or failed scraping operation.
4. Interruption of the welding cycle
An interrupted welding cycle leaves the joint incomplete and unfit for use. This problem occurs mainly due to technical or power problems on the welding machine.
- Sudden shutdown of the power supply to the welding machine.
- Technical problems on the welding machine.
5. Damage to the crystal lattice in the melting zone of materials
If the joint cooling process is not carried out properly, the material’s crystal lattice does not form correctly, making the joint brittle.
- Attempts to quickly cool the joint with water or compressed air (prohibited practices).
- Handling of the joint before the end of the cooling phase.
6. Molten Material Leak from the Joint
The leak of molten material from the joint is an evident sign of an anomaly in the welding process, often related to excessive heat or pressure during fusion.
- Incorrect transfer of fusion parameters to the welding machine.
- Use of pipes with incorrect dimensional tolerances.
7. Damage to the electrical coils of the fitting
Damage to the electrical coils of the fitting can occur when the supply voltage exceeds allowable levels, causing overheating and deterioration of internal electrical components.
- Supply voltage higher than expected.
Note: It is rarely possible to correct errors during the electrofusion welding cycle. If you notice a problem, the only solution is to stop the process, cut off the part that was being welded and start the whole process again from the beginning.