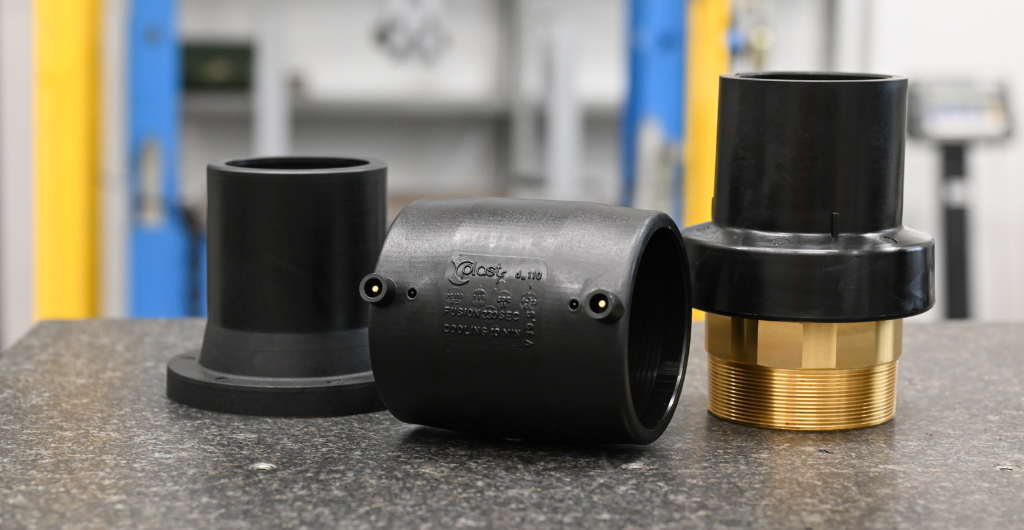
Polyethylene (PE) pipe fittings play a crucial role in modern fluid transport systems across many industries. Thanks to their chemical stability, flexibility, and resistance to harsh environments, PE fittings are increasingly chosen for both new infrastructures and upgrades to existing systems.
In this article, we explore the properties of polyethylene, the different types available, and why it remains a leading material for industrial piping systems. Understanding the advantages of PE materials helps decision-makers select the best components for sustainable and efficient projects.
Understanding Polyethylene in Industrial Piping
Polyethylene is a thermoplastic polymer widely used in piping solutions due to its excellent balance of mechanical strength and chemical resistance. Its versatility allows it to be molded into various shapes and specifications, making it ideal for a wide variety of system requirements in industries such as water treatment, gas distribution, industrial cooling, and critical infrastructure projects.
Thanks to its adaptability, polyethylene has become one of the preferred materials for modern fluid management systems. It offers a reliable, cost-effective alternative to traditional materials like metal or rigid plastics, particularly in applications where environmental stress, chemical exposure, and mechanical loading are key concerns.
What Is Polyethylene (PE)?
Polyethylene is a polymer produced by the polymerization of ethylene gas. It is characterized by its lightweight structure, high chemical resistance, and impressive durability. Different manufacturing processes allow the production of polyethylene variants suited to various technical and operational needs.
In piping systems, polyethylene is valued not only for its mechanical properties but also for its ease of handling and installation, significantly reducing operational costs over time. Its ability to be welded securely ensures leak-free joints, improving system safety and efficiency over decades of service.
Additionally, the smooth internal surface of PE fittings promotes steady fluid flow, minimizing pressure drops and energy consumption within the system. This advantage makes PE a material of choice for engineers seeking efficient and reliable pipeline performance, particularly in large-scale infrastructures where flow optimization is crucial.
The wide operating temperature range of polyethylene, coupled with its resilience to UV exposure (especially in black, UV-stabilized grades), further enhances its appeal for both above-ground and buried installations across different environmental conditions.
Key Physical and Chemical Properties
Polyethylene exhibits a unique combination of attributes that make it superior to many alternative piping materials:
- High flexibility without compromising structural strength, allowing absorption of mechanical stresses and ground movement without cracking.
- Excellent resistance to chemical agents, including solvents, gases, and aggressive industrial fluids.
- Low coefficient of friction, promoting smooth, energy-efficient fluid transport with reduced pumping costs.
- Strong impact resistance even at low temperatures, maintaining integrity in cold climates or challenging installation environments.
- Lightweight nature, simplifying handling, transport, and on-site welding operations.
- Long service life under demanding conditions, typically exceeding 50 years in properly designed and installed systems.
These properties make PE an ideal material for both underground and exposed installations, maintaining consistent performance despite external challenges such as soil movement, pressure variations, temperature extremes, or chemical exposure. The combination of strength, flexibility, and resistance ensures that polyethylene remains one of the most versatile and reliable choices for fluid handling systems worldwide.
Differences Between LDPE, HDPE, and PE100
Although polyethylene comes in different forms, each variant is tailored to specific applications, depending on density, strength, and pressure requirements.
Choosing the correct type of polyethylene is fundamental to ensuring the efficiency and safety of the piping system, especially in environments where operational demands and exposure to external stresses vary significantly.
Material Density and Mechanical Strength
- LDPE (Low-Density Polyethylene): Characterized by high flexibility and lower tensile strength, it is best suited for low-pressure systems, such as temporary irrigation setups or protective pipe couplers. Its softness and ease of handling make it practical where ease of installation and moderate performance are acceptable.
- HDPE (High-Density Polyethylene): Offers greater rigidity and mechanical strength, making it the material of choice for high-pressure systems and critical infrastructure. It performs reliably even under significant external loads and internal pressures. Additionally, HDPE provides excellent resistance to chemicals, UV radiation, and environmental stress cracking, ensuring longevity in outdoor and buried applications.
- PE100-RC (Resistance to Cracking): A premium class of HDPE with enhanced strength and durability, PE100-RC fittings are engineered for the most demanding applications, including potable water systems, natural gas distribution, and industrial pipelines requiring long-term resistance to mechanical and environmental stresses. PE100-RC also offers better hydraulic performance due to its superior density-to-strength ratio, optimizing fluid transport across large distances.
Understanding these distinctions allows engineers to select the appropriate material grade for each project, balancing cost, durability, and performance requirements. Moreover, correct material selection can significantly reduce maintenance costs and enhance system reliability over decades of operation.
Best Use Cases for Each Type
LDPE fittings are typically used in garden irrigation, low-pressure drainage systems, and short-term fluid transport networks where flexibility is more critical than mechanical strength. In these contexts, quick installation and adaptability to movement are prioritized over high mechanical loads.
HDPE fittings are extensively applied in urban water networks, industrial cooling pipelines, and pressurized gas distribution systems, where durability and reliability are crucial. Their ability to withstand external forces and maintain performance under dynamic conditions makes them indispensable for critical public and industrial infrastructures.
PE100-RC fittings are recommended for infrastructures requiring compliance with the highest international standards, such as city-wide water supply systems, high-pressure gas pipelines, and critical facilities like hospitals and data centers. Their superior mechanical properties ensure high safety margins and long-term system sustainability, even under the most challenging operational scenarios.
Advantages of Using Polyethylene Pipe Fittings
The adoption of polyethylene fittings brings numerous technical and economic advantages that enhance the value and longevity of infrastructure projects. Their intrinsic properties make them particularly suitable for installations where durability, flexibility, and safety are essential to maintaining system integrity over time.
In addition, polyethylene fittings provide design flexibility, allowing engineers to create complex piping systems that can adapt to site-specific challenges, such as uneven terrain, urban congestion, or restricted spaces.
Corrosion Resistance and Chemical Stability
Polyethylene fittings offer outstanding resistance to corrosion, eliminating the risk of rust and degradation found in metal systems. They remain stable even when exposed to aggressive chemical agents, including various industrial gases, acids, and alkaline substances. This property ensures a consistently safe transport of fluids over extended periods, reducing maintenance needs and avoiding costly system failures.
Moreover, polyethylene is unaffected by micro-organism growth, protecting the integrity of fluid systems, especially in potable water and wastewater systems where biofilm formation or internal fouling could otherwise compromise performance. This chemical inertness contributes to maintaining high flow efficiency and water quality standards over the operational life of the installation.
Flexibility and Impact Resistance
Flexibility is one of the core strengths of polyethylene. PE fittings can endure soil movement, seismic activity, and mechanical impacts without cracking or breaking. This inherent flexibility allows for longer pipe sections with fewer joints, minimizing potential weak points and installation time.
Additionally, the impact resistance of PE at low temperatures makes it a preferred choice in regions experiencing harsh winters, where traditional materials might become brittle and prone to failure. This resilience also allows for safer transportation, easier handling on-site, and fewer risks of damage during installation or subsequent ground settlement. The combination of strength and adaptability is a key factor behind the growing preference for polyethylene systems in modern civil and industrial projects.
Industrial Applications of Polyethylene Fittings
Thanks to its exceptional combination of properties, polyethylene is used across a wide range of industries and sectors that demand reliability, longevity, and operational efficiency. Its adaptability to different pressures, temperatures, and chemical environments makes it a highly versatile solution for both standard and critical infrastructure projects.
Water and Wastewater Treatment
Municipalities and private companies rely on PE fittings for potable water distribution and wastewater treatment because of their excellent chemical inertness and mechanical durability. These systems must remain leak-free and contamination-resistant for decades, and polyethylene fittings meet these demands while providing easier installation compared to metallic alternatives.
Moreover, the flexibility of PE systems allows for quicker adaptation to topographical changes and easier maintenance interventions when necessary, reducing downtime and lifecycle costs. Their long-term resistance to internal scaling and external chemical attack further supports the operational continuity of essential services.
Gas Transmission Systems
In the gas sector, safety is paramount. PE100 fittings are specifically designed to withstand high internal pressures and resist gas permeation, ensuring the secure and efficient delivery of natural gas to residential, commercial, and industrial consumers. Their performance under fluctuating pressure and temperature conditions makes them the material of choice for critical gas infrastructure worldwide.
The ease of welding and jointing PE100 fittings also minimizes the risk of leaks, providing an additional safety guarantee compared to more traditional materials. Their lightweight nature simplifies installation logistics, particularly in remote or difficult-to-access locations.
Cooling Systems in Data Centers
Data centers require efficient, reliable, and safe cooling solutions to protect sensitive equipment. HDPE piping systems, complemented by high-quality polyethylene fittings, offer excellent flexibility, chemical resistance, and ease of installation, making them ideal for liquid cooling applications in these critical environments.
Their long service life and minimal maintenance needs contribute to maximizing uptime and operational efficiency, critical factors in industries where even minimal downtime can have substantial operational and economic impacts.
In addition, polyethylene’s low thermal conductivity properties help optimize cooling processes, reducing energy consumption and supporting sustainability initiatives in the data center sector.
Conclusion: Why Polyethylene Remains a Key Material for Modern Piping Systems
Polyethylene pipe fittings represent a benchmark in modern infrastructure solutions, offering a rare combination of durability, flexibility, and chemical resistance. Whether used in water supply, gas distribution, or industrial cooling, their reliability and performance ensure sustainable infrastructure with lower maintenance and operational costs.
By understanding the different types of polyethylene and their specific strengths, engineers and decision-makers can optimize system design and execution, achieving safer, more efficient, and longer-lasting results. With continuous innovation in material science, polyethylene remains firmly positioned as a key material for the future of fluid transport systems.