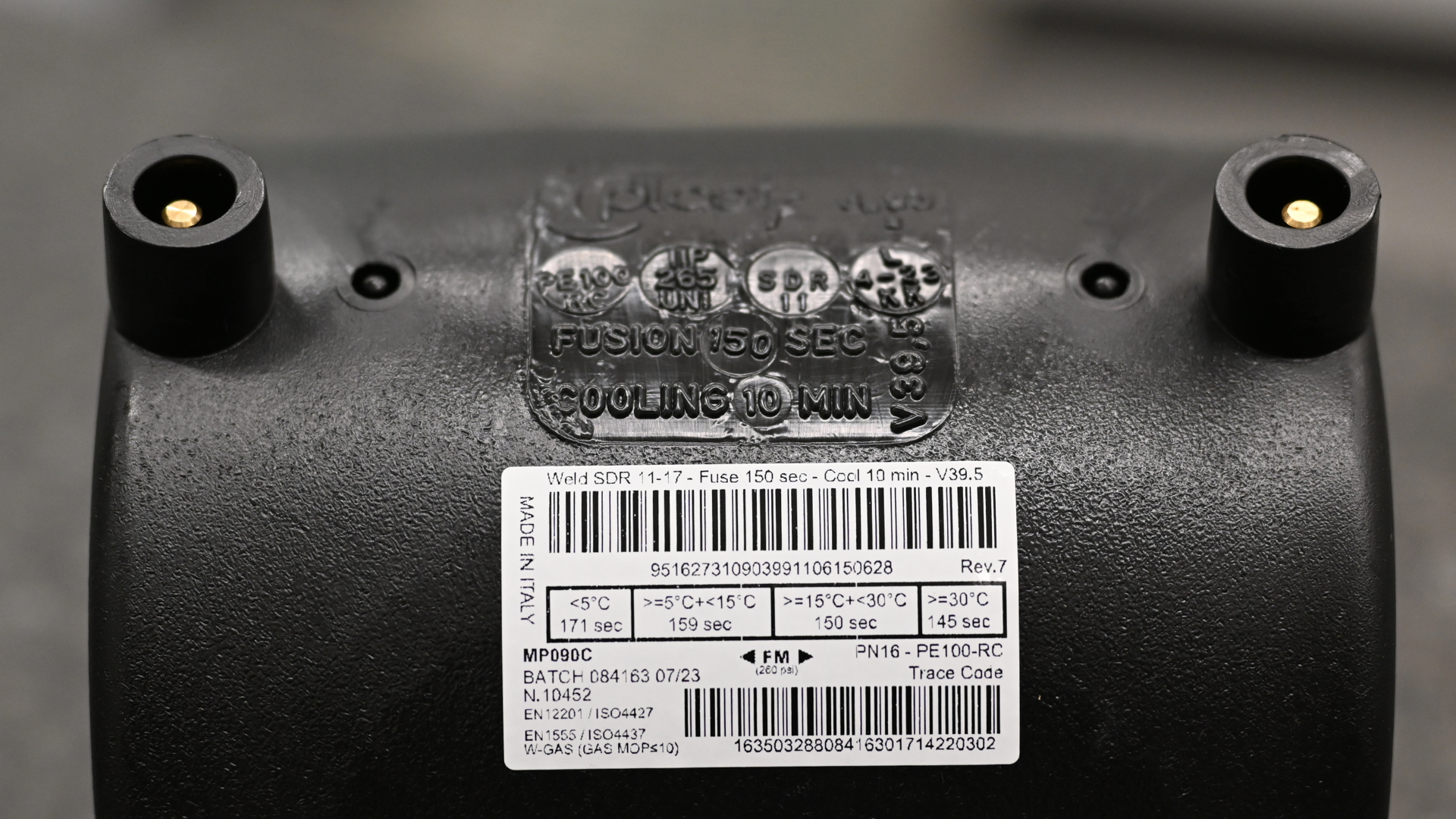
Electrofusion fittings are key components in the installation and maintenance of polyethylene (PE) piping systems, which are used to transport gas, water, and pressurized fluids. Due to their reliability and safety, electrofusion fittings are widely used across several industrial and civil applications. These fittings are manufactured from polyethylene and come in various items (couplers, elbows, tees, etc…) each designed to meet specific requirements. Electrofusion fittings are manufactured in different diameters and can handle varying pressure ratings, depending on the purpose of its use. In this article, we will explore in detail how electrofusion fittings are made, how they work and highlight their key characteristics and processes that ensure safe and durable joints.
Structure and Functions of an Electrofusion Fitting
An electrofusion fitting is a polyethylene product that incorporates an internal stop¹ for the insertion of the pipe – ensuring greater welding accuracy – and a copper coil². The coil is wound around the inner circumference of the fitting and it is the key element of the fusion process. Electrofusion fittings are equipped with pins³ that allow connection to a welding machine. This machine, powered by current generators, transfers electrical energy to the copper coil embedded in the fitting. As the electrical current passes through the copper coil, heat is generated, which melts both the inner polyethylene of the fitting and the outer surface of the pipe in contact with it. This heat causes the polyethylene to expand, generating what is known as welding pressure. This internal pressure pushes the material toward the edges of the coil, where the cooler polyethylene helps block the molten polyethylene, thereby increasing the welding pressure and promoting the co-penetration of the materials. At the end of the melting cycle, it’s time to cool down the elements. During this phase, the molten polyethylene solidifies forming a strong and durable joint.
The fitting’s surface has fusion indicators⁴ which, when raised, visually confirm that the required electrical energy has been correctly applied. However, the presence of these indicators cannot be used as an indicator of the weld quality.
On the external surface of each EF fitting, essential welding parameters⁵ – such as melting and cooling times, raw material used, SDR, diameter, and other technical information – are permanently moulded. Additionally, each electrofusion fitting has a barcode⁶ that includes production and welding parameters. Modern welding machines, equipped with barcode scanners, can read this code automatically setting the correct welding parameters and reducing the risk of errors.
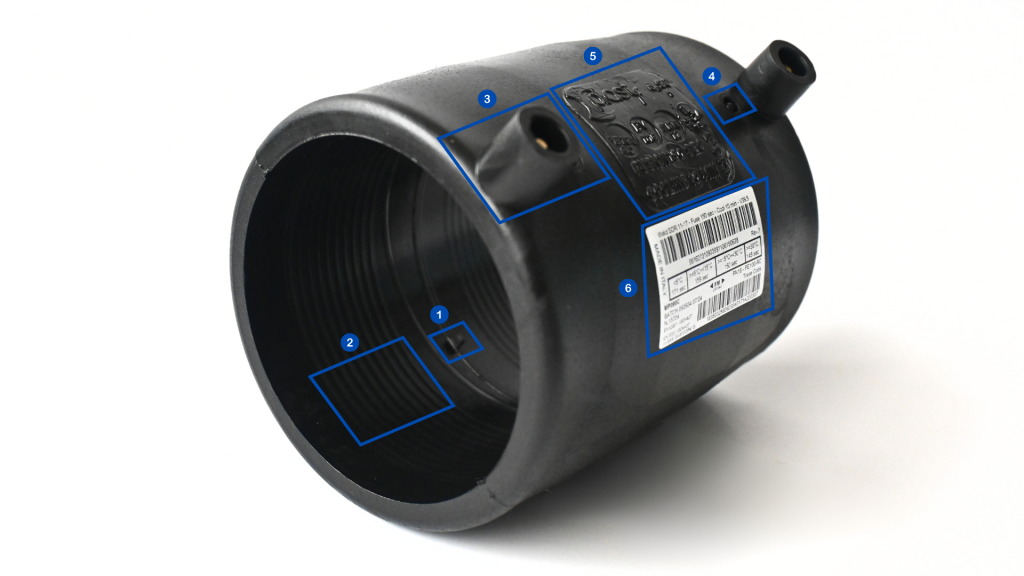